Aerospace Manufacturing
Bar Feeders
Whether you’re turning fuel system components or parts for seat assemblies, precision and speed are prerequisites for success. For businesses in aerospace manufacturing, bar feeders make an important contribution to both.
Bar feeders can increase productivity and add capacity, but only if matched to the task. In aerospace parts manufacturing, there are no “one size fits all” solutions.
IEMCA makes the widest range of machines in the bar feeder industry. Whatever your preferred lathes or Swiss turning machines, bar materials, bar lengths, and cutting speeds, there’s a machine to suit. Our bar feeder search tool can help you find exactly what you need. We also sell used bar feeders.
Bar Feeders for the Aerospace Industry
In aerospace manufacturing, every piece machined must conform precisely to the specifications. That’s why businesses make sure to follow AS9100 and Nadcap procedures and requirements. It’s also why they use high-quality machines that deliver consistent performance.
Bar feeder machines for aerospace applications handle the full range of materials used — from stainless and aluminum to titanium and superalloys. “Standard” capacity of a bar feeder is the 12-foot bar. However, IEMCA can offer longer and shorter options to suit shorter runs or footprint constraints. In terms of bar size, machines are available for diameters from 0.8 millimeters to 100 millimeters.
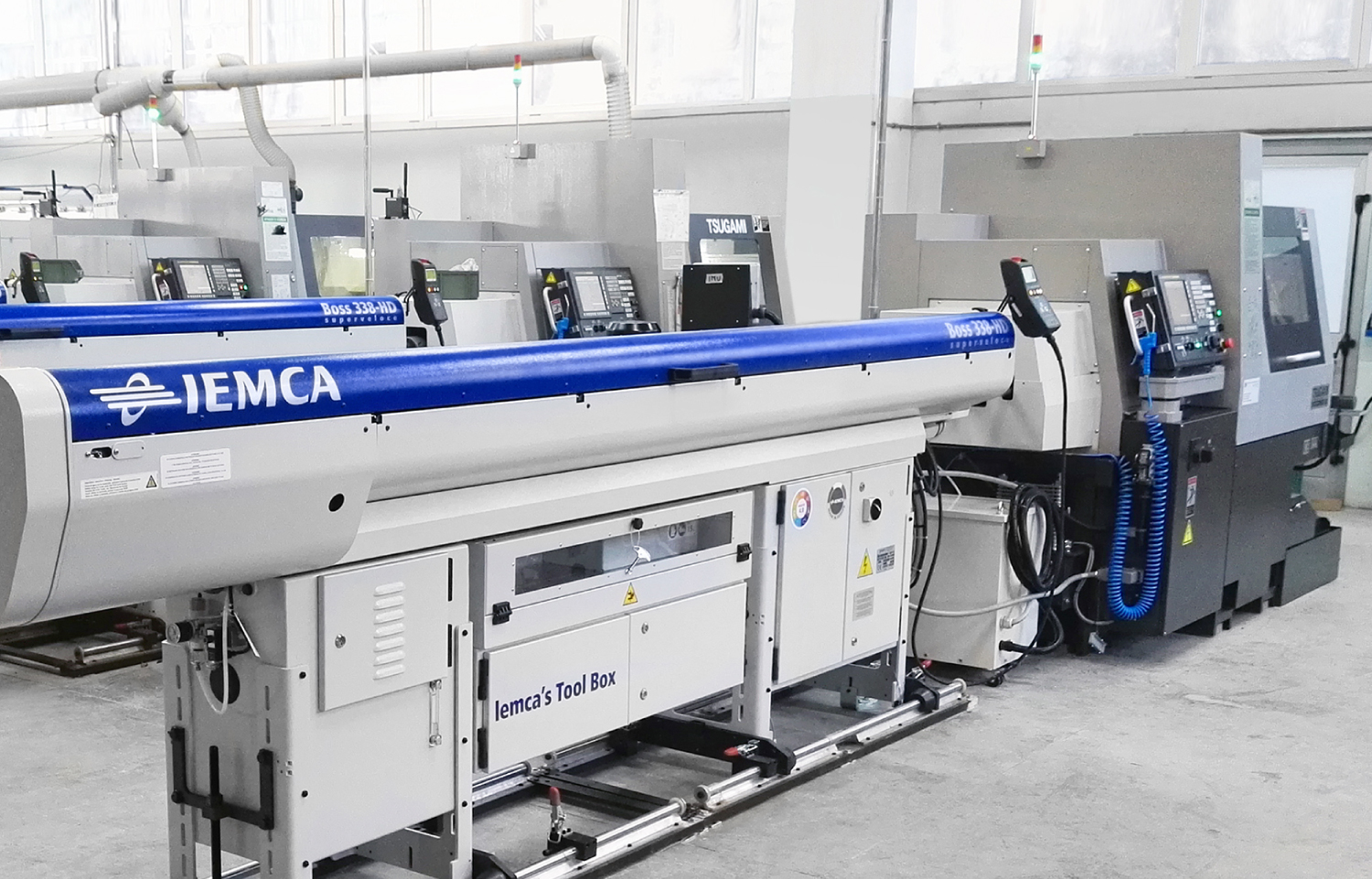
Tsugami BO325 and IEMCA Boss 338
Parts Turned on Aerospace Bar Feeder Systems
Aerospace manufacturing volumes range from one-offs for space and satellite applications to the high volumes of seats and fuel system subassemblies required by commercial aircraft builders.
Parts coming off multi-spindle lathes, Swiss-style machines and regular CNC turning centers include:
- Retainer rings
- Check valves
- Special fasteners
- Guidance system components
- Seat components
- Cargo tie-down parts
- Connectors
- Flanges
- Couplings
All these components are candidates for aerospace bar feeder systems.
Benefits of Bar Feeders for the Aerospace Industry
By indexing a length of bar material through the headstock, a bar feeder eliminates manual loading of a chuck or collet. It’s also faster than robot loading and unloading. This minimizes the time for which a machine is stopped, which increases productivity.
The benefits this leads to include:
- Higher lathe OEE
- Lower labor content per piece produced (when one worker tends multiple machines)
- Increased turning capacity (take on more work or reduce the area dedicated to turning)
- Higher material utilization (the only waste is the bar remnant as opposed to every piece having a stub gripped in the chuck or collet)
In addition, bars vibrate as they rotate. A bar feeder that does a good job of smoothing this vibration, such as those from IEMCA, enables higher spindle rpms than an inferior quality machine.
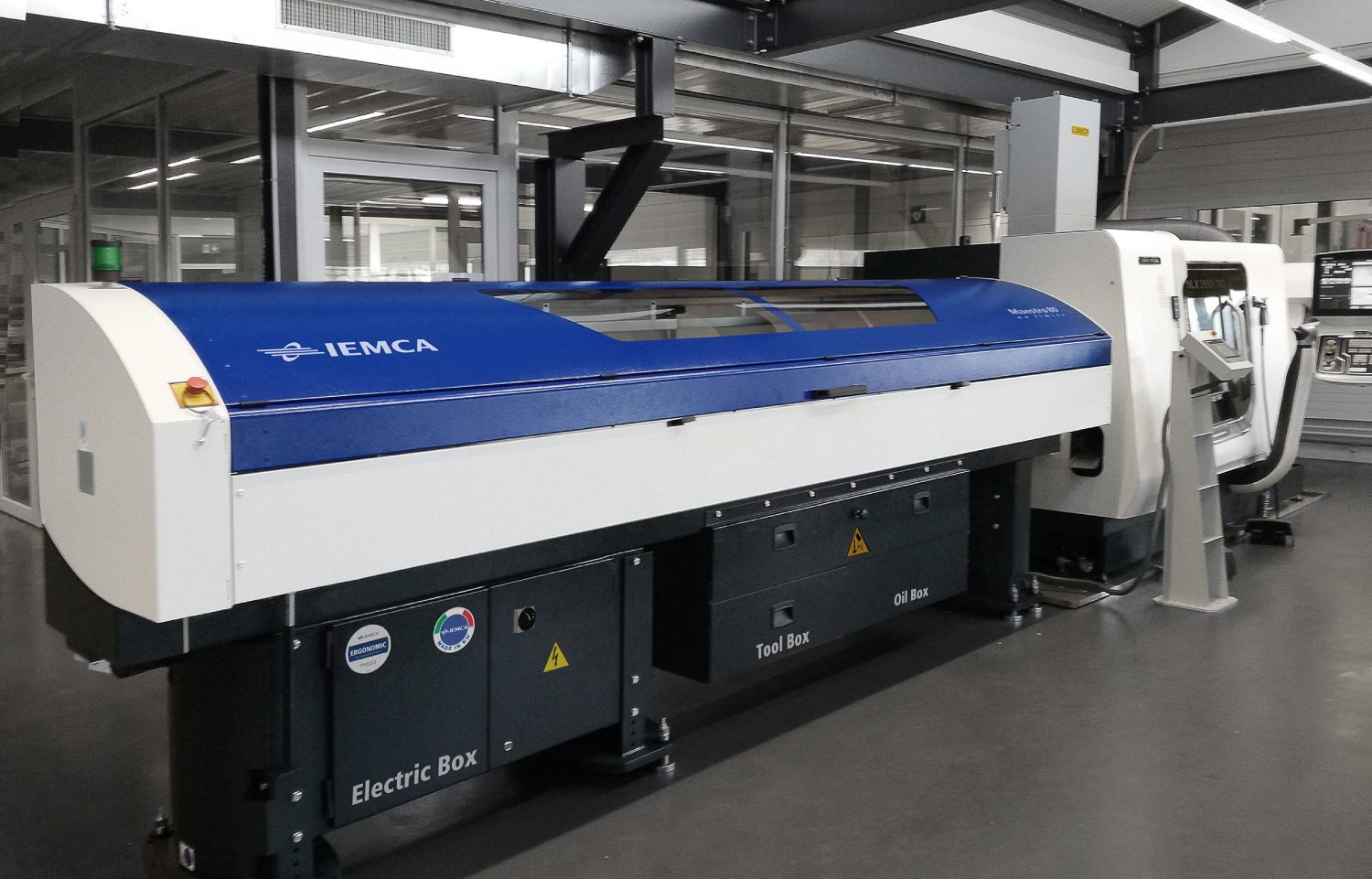
DMG Mori CTX alpha 500 and IEMCA Maestro 80
Choose IEMCA for Aerospace Manufacturing Bar Feeders
IEMCA invented the automatic bar feeder in 1961. Since then, we have sold thousands to manufacturers around the world. Today, in addition to our original location in Faenza, Italy, we have production in the USA, China and Taiwan. With a workforce of more than 500, every employee is committed to listening to our clients so we can provide the best solutions for their needs.
Search our products or contact us to find out how we could help improve your turning productivity.