In mechanical machining on fixed headstock lathes, the generation of vibrations cannot be avoided: what matters is knowing how to adjust the setup to manage and minimize them.
It is, in fact, a natural phenomenon linked to the dynamics of interaction between the spindle system, the cutting tool, and the workpiece. If not properly controlled, vibrations can compromise the surface finish quality, reduce tool life, damage the spindle, and, more generally, negatively impact overall productivity.
To properly manage vibrations, it is essential to understand the variables that influence their generation. Among these, an often underestimated element is the bar feeder chosen to accompany the fixed headstock lathe – in particular, the characteristics of its bar guiding system.
Why the bar guiding system is crucial in fixed headstock machining
On fixed headstock lathes, long, large-diameter bars are often machined: even minimal instability can generate significant vibrations. For this reason, the bar feeder’s guiding system plays a fundamental role in ensuring the bar stability and reducing vibrations throughout the entire machining cycle.
An effective guiding system can adapt as closely as possible to the bar diameter, guiding it smoothly during rotation to minimize oscillations and misalignments.
An optimal guiding system does more than contain the bar: every single detail must be designed to actively absorb and dampen vibrations, protecting the machine and preserving the final part quality. High-damping material, a diameter-adjustable bar guide channel, and intermediate guiding points between the bar feeder and lathe: all these elements contribute to improving the setup and its ability to manage vibrations.
ABACOS: the flexible guiding system for fixed headstock lathes
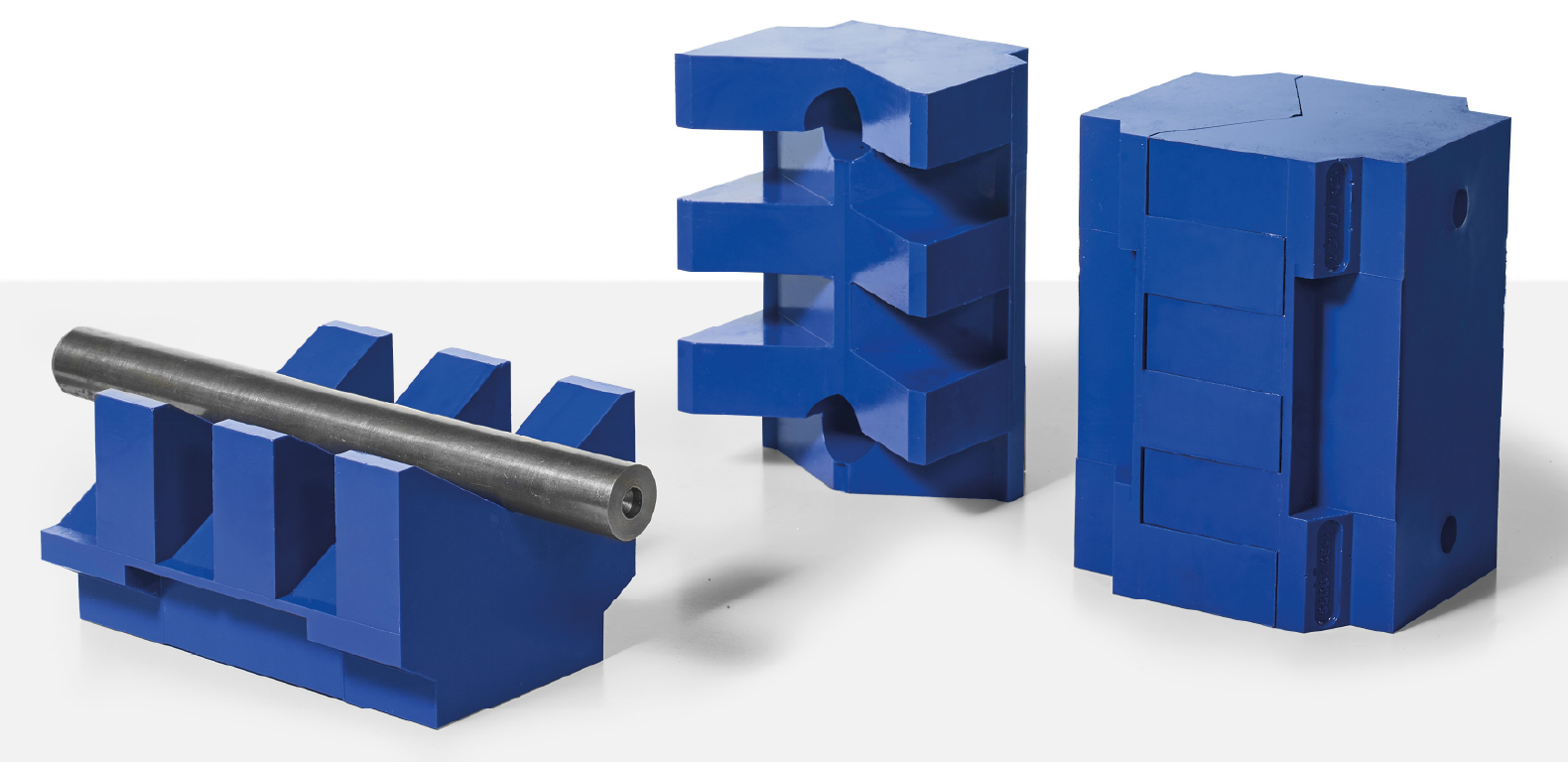
The bar feeders for fixed headstock lathes IEMCA MAESTRO are designed to ensure optimal guiding of the bar inside the spindle, even in the most complex and demanding applications. Special attention has been given to developing an effective solution for vibration management.
The MAESTRO range is equipped with the patented IEMCA ABACOS (Adaptive BAr COntrol System), which uses self-adjusting bushings that adapt to the machined bar diameter.
- The self-adjusting bushings automatically adapt to the diameter, guiding the bar optimally throughout the entire machining cycle.
- Thanks to the innovative bushing design, the ABACOS system provides 4 constant-length contact points with the bar (regardless of diameter) and ensures precise, effective support.
- The system features a lubrication circuit that reduces friction between the bushings and the bar, ensuring smoother rotation.
- The integrated pneumatic system actively absorbs vibrations generated during machining, minimizing their impact on the setup.
- The bushings are made from a material specifically engineered to dampen vibrations.
- The ABACOS system can tighten the bar pusher, automatically adapting to its diameter: any potential disturbance is neutralized, ensuring maximum stability throughout the production cycle.
Less vibrations, greater productivity: the benefits for your headstock lathe
Thanks to the ABACOS system applied to the MAESTRO bar feeders for fixed headstock lathes, the vibrations generated during machining are kept under control, increasing productivity and precision of the operation.
Less vibration means better surface finish and part quality, reduced tool wear, and increased reliability and productivity of the entire setup.
Find out how MAESTRO can optimize your fixed headstock machining: contact our team for a dedicated consultation.