The use of high-pressure coolant fluid significantly improves the performance of a machine tool and increases the overall productivity of bar-fed turning applications. It directly addresses factors that can affect the efficiency, performance, and quality of mechanical processes, including bar turning.
The coolant fluid serves two distinct functions: it cools the working area, where friction between the tool and the workpiece generates high-temperature heat, and it properly lubricates the point of contact between the cutting tool and the workpiece.
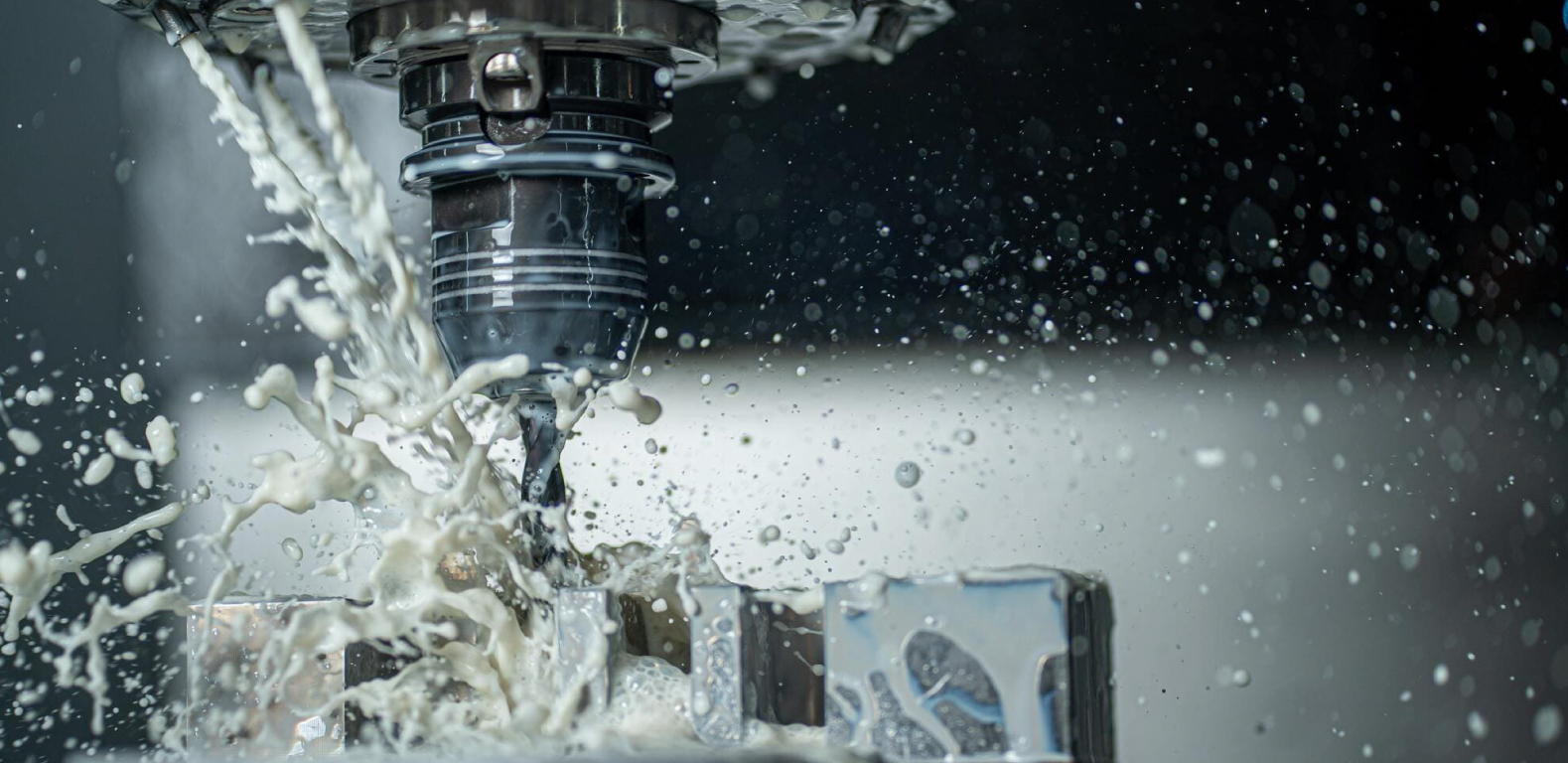
Low-Pressure vs. High-Pressure Coolant Distribution
Low-pressure distribution of coolant often proves ineffective: the heat generated in the contact zone is so high that the fluid evaporates before reaching the cutting tip. It is, therefore, preferable to use high-pressure coolant cutting tools, such as tips with internal coolant delivery and turning tools with targeted nozzles, alongside a high-pressure unit for use with fixed or sliding headstock lathes.
The high-pressure system manages the coolant fluid: it distributes and dispenses the fluid at various pressures, recovers and filters the dirty fluid contaminated by particles generated during processing, and recirculates it.
The pressurized, precise, and targeted jet, optimized based on the pressure and flow requirements of each individual tool, efficiently cools and lubricates the working area. It optimizes chip control and limits heat development, ensuring an immediate increase in the performance and productivity of the turning center.
Optimizing Chip Control with High-Pressure Coolant
Chip control directly influences the efficiency and performance of the machine tool and the entire production process.
The use of high-pressure coolant during turning operations facilitates chip breakage and evacuation and promotes the formation of smaller chips compared to dry or low-pressure processing. Effective chip management significantly reduces machine downtime for maintenance operations, resulting from the accumulation of long chips on the tool and workpiece or the clogging of chip conveyors. Thanks to the cooling action and correct fluid pressure, the working area remains clean and free of residues.
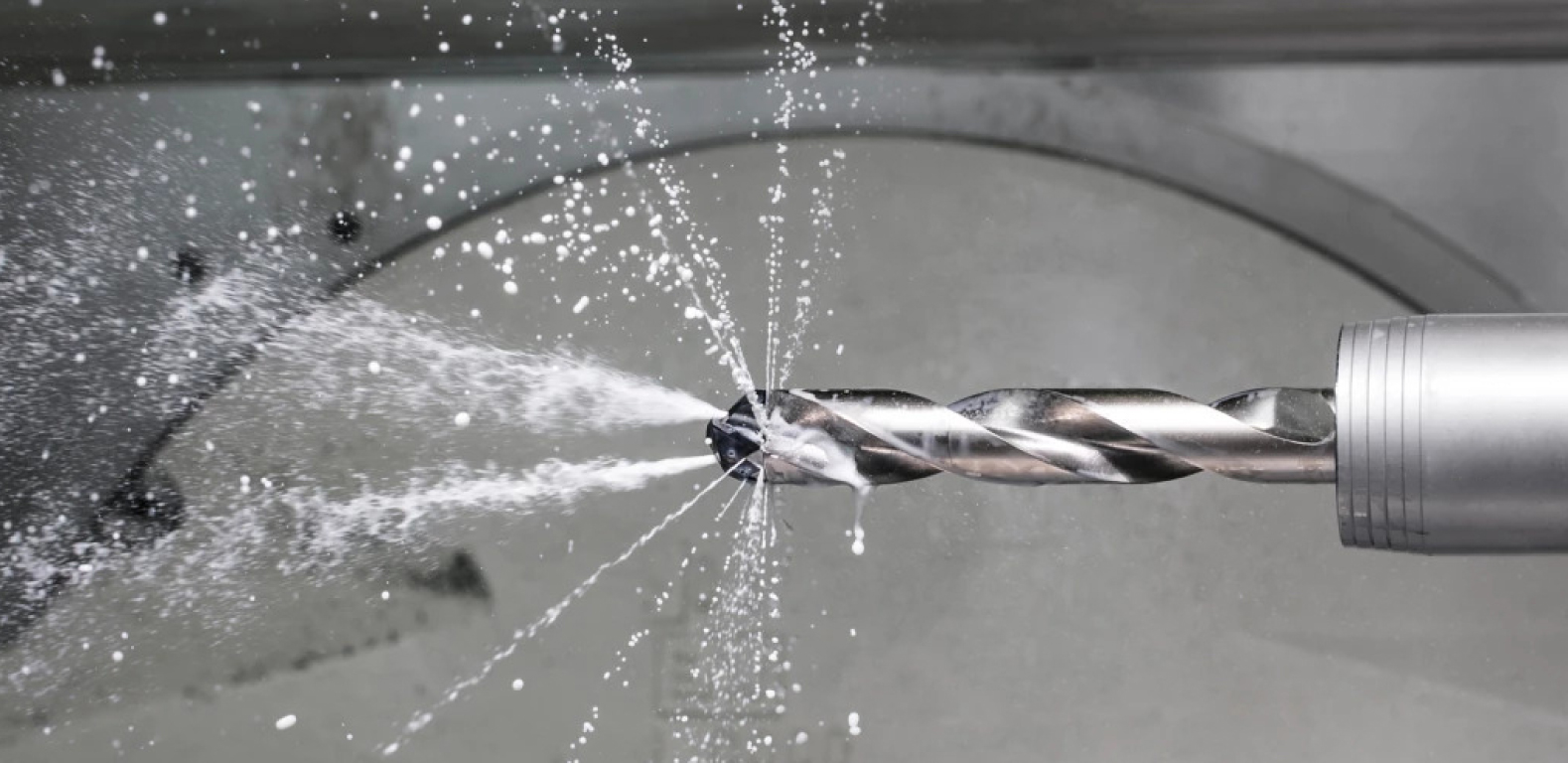
The Filtration System
High pressure requires the use of uncontaminated coolant, free of suspended particles that could obstruct the millimetric passages of pipelines and nozzles near cutting tools, causing damage to the workpiece and tool itself. An advanced and properly sized filtration circuit is crucial for long-lasting, uninterrupted operation. It minimizes unproductive downtime due to cleaning and filter replacement or other maintenance operations due to chip management inefficiencies.
Limiting Heat Development in the Working Area with High-Pressure Coolant
The generation of high temperatures is one of the most impactful factors in turning operations. The use of a high-pressure coolant system significantly reduces heat development.
The targeted jet and controlled pressure effectively cool the cutting zone, preventing the overheating of the tool and workpiece. Lower temperatures bring numerous benefits to the entire process, including proper lubrication, optimized tool performance and lifespan, and an increase in feed and turning speed.
Reducing the heat generated also makes it easier to preserve the structure and properties of the workpiece material, avoiding deformations and damage due to increased temperature, such as thermal expansion that alters the size of the workpiece. This results in higher final component quality, which is particularly important for applications requiring extremely precise finishes.
The Importance of Choosing the Right High-Pressure System for Your Lathe
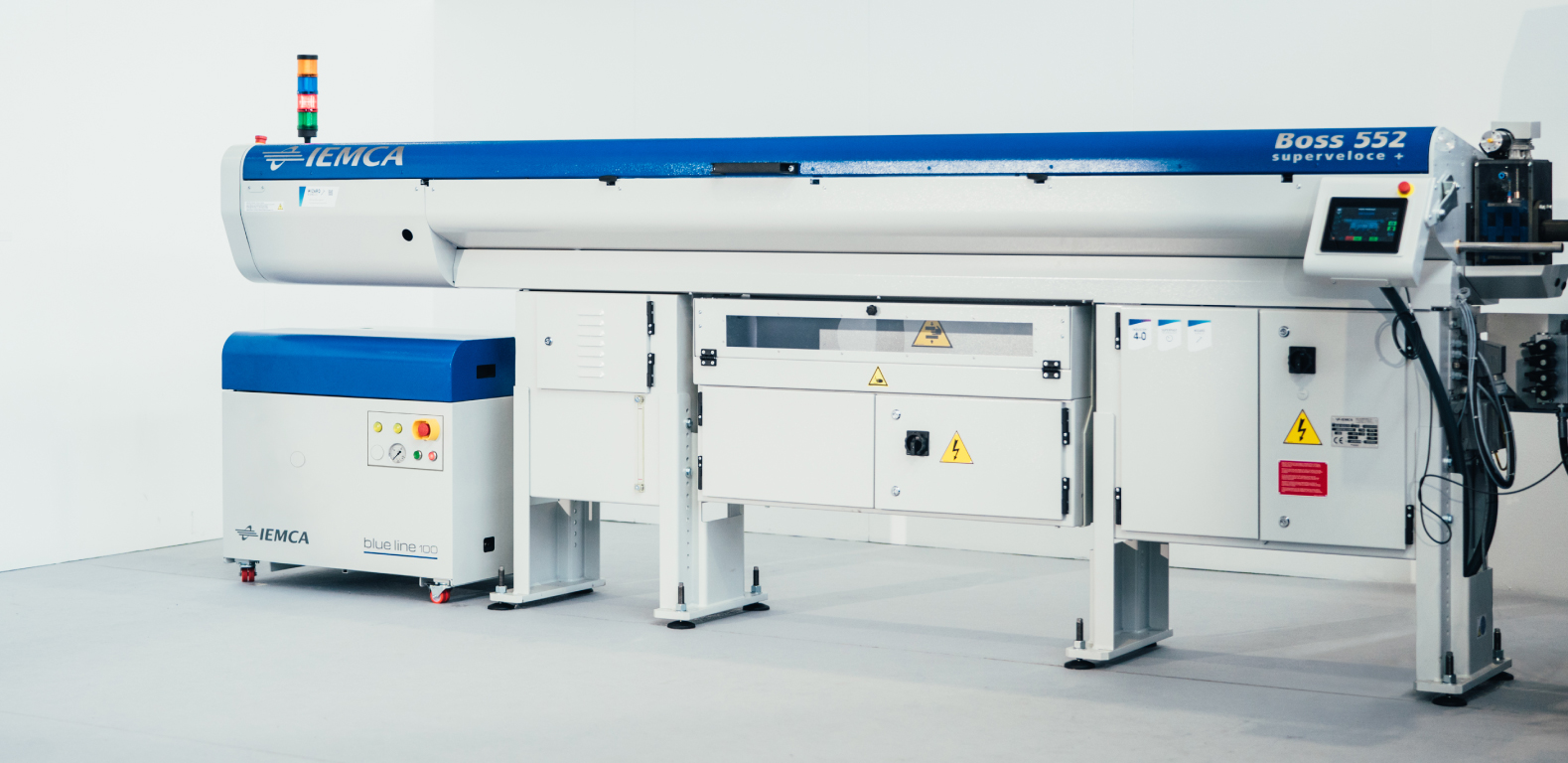
The correct choice of a high-pressure system for managing coolant fluid is crucial for increasing productivity and reducing overall costs in chip removal applications such as bar turning.
Integration with the Bar Feeder
The IEMCA high-pressure system is designed to seamlessly integrate with the bar feeder: its compact size and organized cable and pipe layout allow for installation under the machine, optimizing workshop space. Activity monitoring is done through the same operator panel as the bar feeder.
Simplified Maintenance
The IEMCA Blue Line high-pressure unit features a two-stage filtration system with cartridge filters: the large filter surface optimizes system operation and maintenance interventions, minimizing unproductive downtime.
Maximum Flexibility
Thanks to the use of a vane pump, the coolant fluid can be constantly maintained at pressure within the unit, ready to be recirculated and used, avoiding long waiting times and energy waste. Outlet pressures can also be diversified according to the requirements of each lathe tool, ensuring maximum adaptability and flexibility.
Customizable Configuration
The configuration of the IEMCA high-pressure system can be customized to meet the specific needs of each application, including process-specific requirements, machining type, and material used.
Contact us now to discover how the IEMCA high-pressure unit can improve your production performance.